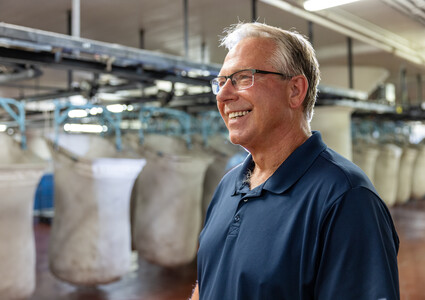
The Meaning of Care Magazine
Shared Service Systems Provides Quality Products for Health Care Facilities Throughout the Region
Published: Aug. 29, 2023
John Perkins started working at Shared Service Systems in 1991 as an environmental services worker.
He worked his way up into leadership roles before leaving in the early 2000s to pursue work as a painter.
After being self-employed for seven years, Perkins received a call from his previous employer asking if he wanted to come back.
Nearly 23 years after getting his start at Shared Service Systems, Perkins was rehired in 2014 as a laundry supervisor in charge of the soiled linen and environmental service teams – a position he’s now held for nine years.
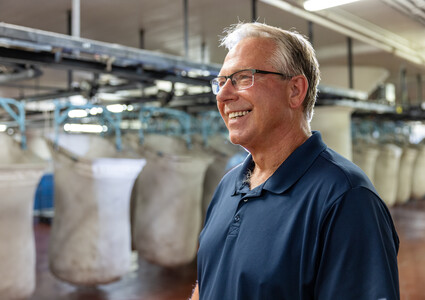
“I was glad to come back because I take pride in what I do,” Perkins said.
That pride is apparent to those who work with him.
“John is one of the more dedicated people I’ve ever been around,” said Steve Pottebaum, director of linen services. “If you put him on a task, it’s guaranteed to get done.”
Providing Quality Products
Shared Service Systems – known by Methodist employees and clients as Shared or Shared Services – opened in 1971 to serve as a central laundry and purchasing hub for Methodist Hospital and Methodist Jennie Edmundson Hospital.
In 1981, John Estabrook, former president and CEO of Methodist Health System, included Shared in his creation of the health system.
Now, more than 50 years after opening for business, Shared offers distribution services for medical/surgical supplies across Nebraska, Kansas and portions of Iowa and Missouri. It stocks more than 10,000 items from over 1,000 manufacturers in its distribution center near downtown Omaha. The products are circulated to 1,200 accounts, including Methodist Health System and many community health care facilities in the region.
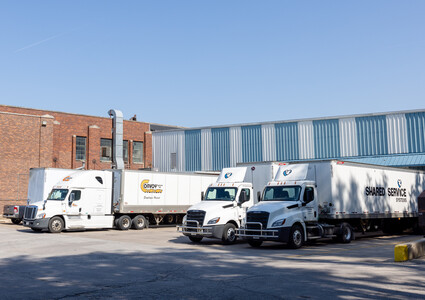
“A hospital’s goal is to provide the best care possible. Our goal is helping hospitals meet that goal with quality products and service,” said Steve Rogers, president of Shared Service Systems.
Shared’s warehouse holds close to $8 million worth of products. It receives product during the morning hours, fulfills orders throughout the day and sends out product at night – about $250,000 worth each night, Monday through Friday.
“We’re so grateful to have Shared Services as a part of our Methodist family,” said Josie Abboud, president and CEO of Methodist Hospital and Methodist Women’s Hospital. “Every day in our hospitals, we provide lifesaving, high-quality care. Shared provides us the necessary supplies to ensure that our teams can provide this care and respond to emergencies without delay.”
Additionally, Shared’s centralized laundry service supplies clean linens for nearly 100 accounts – hospitals, medical clinics and retirement homes – within a 150-mile radius.
About 125,000 pounds of laundry – all owned by Shared – is completed on a weekly basis, including more than 75,000 pounds from Methodist Hospital, Methodist Women’s Hospital, Methodist Jennie Edmundson Hospital and Methodist Physicians Clinic.
Katie Houdek, BSN, RN, the nurse coordinator for urology and gynecology surgical services at Methodist Hospital, believes that having an ample supply of clean blankets and towels is one of the ways her team can provide comfort for patients.
“And we don’t have to worry about if it’s going to be there,” she said. “We just know that it’s going to be.”
Sorting the Soiled
As supervisor of the soiled linen team, Perkins oversees the process of making sure the dirty laundry is organized before being washed.
Within a day or two of arriving via a Shared truck, the laundry is weighed and marked in a log before being placed on a conveyer belt to be sent for sorting.
In the sorting area, up to five people organize the laundry into different bins. After a bin is filled, the linen moves on another belt that drops it into a bag. The bag – holding about 100 pounds of laundry — then moves toward a chute where the laundry falls into a large washing machine.
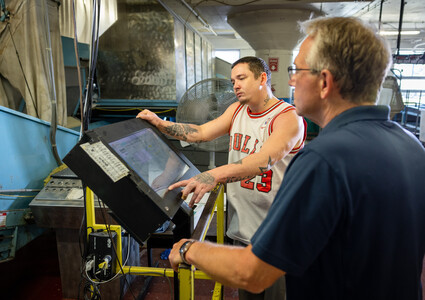
Melinda Reineke, a laundry sorting technician, understands that working quickly is essential to the start of the washing process.
“You go as fast as you can, looking for the specific things,” she said. “We need to get done with what they’re bringing in. You have to meet your customers’ needs.”
Occasionally, Perkins receives a call saying that a non-laundry item has been lost within a shipment of linens. Because each shipment is tracked, the sorting team is able to go through a specific order to search for the missing item.
“It’s like a scavenger hunt,” Reineke said. “So it’s kind of fun.”
Some of the more significant items that have been retrieved are diamond rings, gold necklaces, watches, cell phones and wallets.
“It’s important to get things back to who they belong to,” Perkins said.
Completing the Job
About 215 loads of laundry are completed daily using two 13-chamber tunnel washers. It takes about 30 minutes for a 100-pound load of laundry to make its way through the full length of a tunnel washer as a different chemical is applied in each chamber.
After the linens make their way through the tunnels, the water is pressed out rather than extracted or spun out like a traditional washer. Then it’s on to the dryer.
In addition to the tunnel washers, Shared uses three heavy-duty conventional washers for heavily soiled items and other specialty items.
Lab testing is completed regularly to ensure that the product being sent out surpasses cleaning standards for commercial laundry.
After the linen goes through the washing and drying process, it’s then sorted to either be folded or ironed. Items like sheets and washcloths are sent through iron machines, while scrubs and gowns are sent directly to an area for hand folding and sorting.
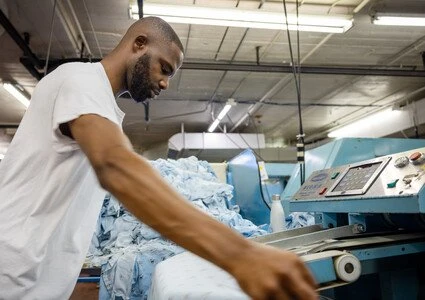
Once pieces of linen are ironed and folded, they’re placed in large metal crates that are weighed to make sure orders are filled correctly before moving to the loading dock to be picked up at night.
All of the linens are delivered with medical/surgical supplies directly to hospitals and clinics on Shared Service Systems semis and box trucks. Methodist’s hospitals receive shipments daily, while smaller accounts such as rural hospitals may receive a shipment only once a week.
“Everything I need to help care for the patient is always going to be there, every day,” Houdek said.
The availability of clean sheets and blankets in each patient room doesn’t go unnoticed.
“The quality of sheets and blankets were great!” said Maysen Lake, who delivered her first child at Methodist Women’s Hospital. “We never had to ask for extra because the cupboards were always stocked with what we needed.”
“It’s essential that our linen services provide an adequate supply of clean linens that are high quality and exceed infection prevention standards for the comfort and safety of our patients,” Abboud said. “Shared may be a ‘behind-the-scenes’ service, but it is very much an integral and vital part of our patient care.”
Perkins understands the importance of Shared’s role within the health system.
“If we do our job, then it’s less stressful on everyone else.”
Photos by Dan Johnson
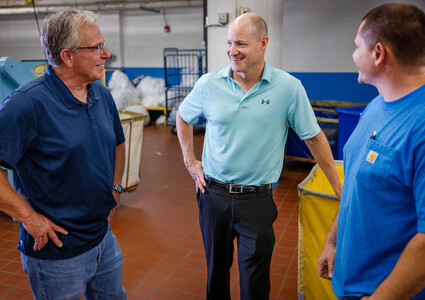
More Resources
- Read more from the summer 2023 issue of The Meaning of Care Magazine.
- Visit the Shared Service Systems website.